精炼炉冶炼过程中低碳钢增碳行为措施
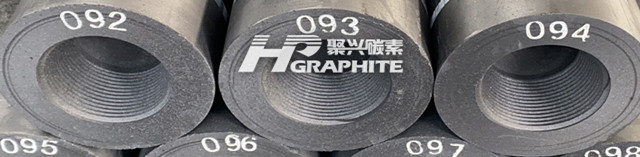
1 针对低碳钢增碳采取的措施
应用底层事件分析结果,结合冶炼工艺可控状态及难易程度采取措施如下:
(1)调整导电支臂倾角,使电极 ABC 三相倾角 相同,电抗平衡(表 6), 石墨电极产品信息详情。
(2)调整底吹氩气孔角度,由 75°调整到 150°, 如图 3。
双孔轴对称底吹法(图 3(a))与双孔中间对称 底吹法图 3(c)在精炼钢包炉应用各有优缺点。 双孔轴对称底吹法优点是钢水表面流动速度快、混匀时 间相对短、去夹杂快,但由于不同温度钢水的黏度 系数不同,底吹氩气流量不容易控制。 而双孔中间对称底吹法的优点在于钢水表面流动速度相对慢,混匀时间、氩气流量控制相对容易。 结合双孔轴对称及双孔中间对称底吹法的优点将原有的底吹 75° 夹角改为底吹 150°夹角,见图 3(b)。
(3)调整氩气供应量,氩气供给量从 50~100 m3/ h 调整到 20~40 m3 /h, 减缓了钢水表面的流动速度和泡沫渣对电极的冲刷, 同时克服了卷渣现象,使混匀时间达到极高。
(4)依据低碳钢冶炼需要调整石墨电极配方。 主要调整了大中颗粒配比, 提高了石墨电极高温下抗热冲击能力,减少电极的开裂掉块。 同时采用高温胶涂刷接头的方式使螺纹相互紧密粘接,预防掉落。
针对低碳钢生产改进的石墨电极配方对比表见表 7。
2 实施成效
以上措施实施后收到了显明成效,低碳钢碳超标炉数大幅减少,电极消耗和电耗下降,冶炼时间相对缩短(见表 8)。 改进氩气底吹孔和氩气底吹流量后使钢水死区面积大幅减小,提高了钢水的混匀度。 同时石墨电极孔壁脱落和电极底部偏弧现象也有所改善(图 4)。 通过采取上述措施每月节省电极费用 12 万元,节省电费 25 万元。
3 结论
应用事故树分析方法分析低碳钢增碳行为可以得出如下结论:
(1)低碳钢的增碳行为不但和电极有关,也与冶炼过程控制息息相关。 要减少石墨电极增碳必须在电炉大中修过程中对冶炼设备每一环节进行认真检修,才能使电炉运行状况达到极高,减少增碳现象。
(2)转炉来碳、氩气底吹角度及底吹量对低碳钢增碳的控制也极为重要。转炉来碳高、氩气底吹角度小、 底吹流量大都会影响石墨电极对钢水的增碳行为。
(3)石墨电极对低碳钢的增碳主要是由于电炉中高温下端部起弧,电极中的碳进入泡沫渣中与渣液中的金属氧化物反应生成碳化物进入钢水直接增碳。
(4)目前各炭素厂家还没有专门供给低碳钢冶炼的石墨电极,开发针对低碳钢冶炼的石墨电极也是减少低碳钢增碳的一个方向,获取更多石墨产品行业信息联系我们。
没有找到相关结果
0 个回复