精炼炉冶炼过程中低碳钢增碳行为分析
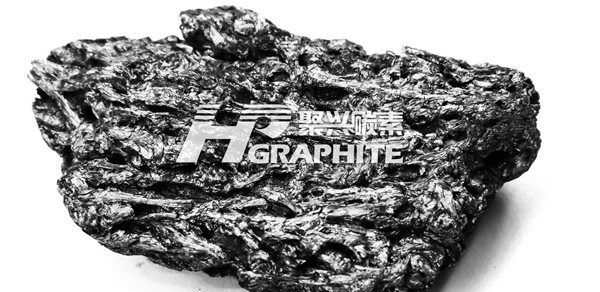
应用事故树分析理论分析冶炼低碳钢过程中精炼阶段低碳钢增碳根源,并给出改进措施:通过调整LF炉设备状况,特别是调整导电支臂倾角,使三相电流电抗平衡,降低电极消耗;通过调整氩气供给量、氩气底吹孔(双孔)的角度使钢水混匀搅拌时间达到最佳最短;调整石墨电极配方中大颗粒比例,使电极开裂掉块现象大幅减少,为低碳钢冶炼过程中降低低碳钢增碳提供技术支撑。
事故树分析方法是美国航天局在上世纪70年代发射火箭为寻找事故点而首创的分析方法。由于该方法不但可以定性分析也可以定量分析,因此在事故预测、事故处理上广泛应用。精炼炉冶炼低碳钢,其核心技术就是控制碳来源。造成低碳钢增碳的原因很多,既有转炉来碳原因,又有石墨电极质量原因,还有精炼包破损镁碳砖增碳及LF炉供电设备、氩气流量、氩气孔角度等原因。因此,在实际生产中想准确找出低碳钢增碳点十分困难。本文采用事故树分析方法,就精炼阶段低碳钢增碳根源进行了分析探讨。
1 应用事故树分析方法分析增碳根源
从实际冶炼工作数据表中提取增碳数据,建立事故树的数据源。
(1)转炉来碳、精炼增碳指标数据提取(表1)
从表1转炉来碳指标可以看出,转炉来碳含量越高越容易造成低碳钢钢水碳超标。无论转炉来碳高低,在共计237炉钢水中增碳幅度0.01%~0.02%占总钢水量的93%以上,说明在精炼过程中钢水增碳现象普遍。
(2)三相石墨电极各相电流、各相消耗及电极倾角数据提取(表2)
从表2三相电极各相电流、各相消耗的数据分析看,A相电极电流高出B相和C相近1.4倍,A相电极消耗高出B相和C相近1.6倍。而引发这一现象的根本原因是电极倾角不同导致的电抗不平衡(A相视为非正常消耗,B相和C相电极视为正常消耗)。
(3)通电时间与低碳钢增碳超标数据提取(表3)
从表3通电时间上可以看出,冶炼通电时间越长,钢水越容易被增碳。冶炼时间小于16min时碳超标炉贡献率为0,因此可视16min内增碳为正常增碳 获得更多石墨信息咨询我们。
(4)氩气底吹流量及底吹角度数据提取(表4)
没有找到相关结果
0 个回复